- Category: Articles
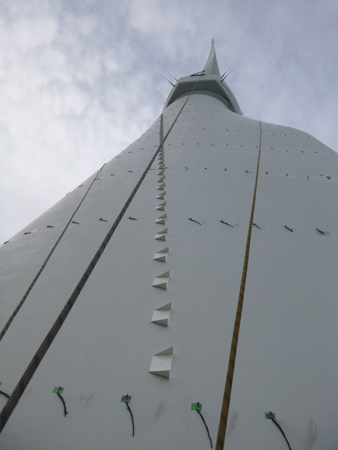
The highest increase in annual yield a wind turbine can obtain is by increasing the rotor diameter. This is because the increase in wind power follows a mathematical ‘power of 2 law’ based on the diameter. For existing blade lengths and for the turbines that have already been running for a while, improvement is also possible by the use of flow changers. The amount of improvement is not to be underestimated and can bring a lot – at least up to 2.5% annual yield.
By Edo Kuipers, We4Ce, the Netherlands
- Category: Articles
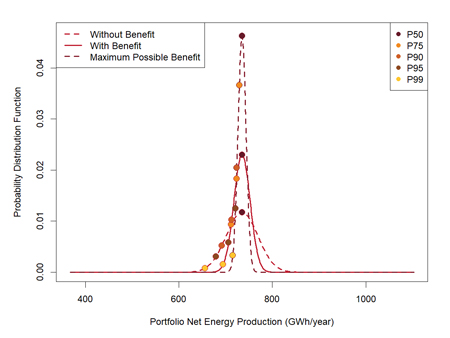
Almost 50% of installed wind capacity in the USA is at least eight years old, accounting for approximately 60GW of operational projects. Unlike greenfield development, these projects have been operating for several years, which provides valuable insight into topics such as project performance, operating costs and revenue, community relations, environmental risks, and other key aspects.
By Jeremy Tchou, Director for Due Diligence, UL, USA
- Category: Articles
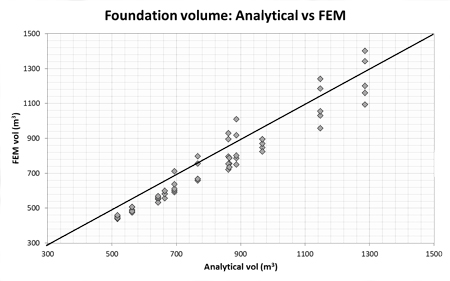
Larger turbines suppose an increase in loads that finally requires more prominent foundations. Those dimensions lead to flexible behaviour. With the current foundation volumes, we are at the boundary of applicability of some analytical expressions widely used in foundation geotechnical and structural calculations, especially in the early stages of design, as they assume the foundation to be a rigid body. Two possible scenarios arise. If the analytical expressions are on the safe side that will lead to overpricing with an overestimated foundation volume. On the other hand, analytical expressions could lead to unsafe foundation design.
By Matias Campos, AZTEC Engineering, USA and Maria Collado, TYPSA, Spain
- Category: Articles
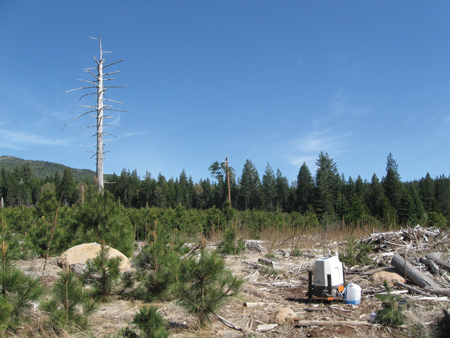
A recent industry poll of almost 1,000 wind industry professionals reported that the remote sensing device (RSD) ‘lidar’ was being used standalone, i.e. without any additional on-site met masts or anemometry, in simple terrain for wind resource assessment in the development of wind energy projects by almost two-thirds of those responding. Much of this confidence can be traced back to the DNV GL ‘Stage 3’ statement in the roadmap for RSDs that allows for a standalone ZX 300 Wind Lidar, since October 2012, to be used in this way. In comparison, when considering the use of any lidar in complex terrain, less than one-third of those responding reported using the lidar standalone; instead, it would be complemented by additional on-site anemometry such as a met mast. In order for the industry to take advantage of the many additional benefits that lidars provide, the challenge was set: how can we as an industry demonstrate the traceability and prove the accuracy of a lidar-only methodology in complex terrain?
By Tristan Clarenc, Johannes Cordes, Alex Woodward, Scott Wylie
- Category: Articles
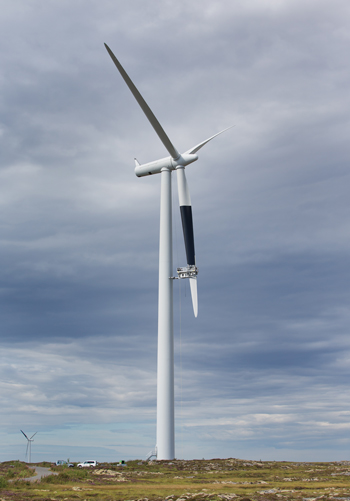
An American research report led to the elimination of eagle deaths on the Norwegian island of Smøla. A review demonstrates that with today’s larger wind turbines, three black turbine blades per wind turbine can give at least as good results as the Norwegian experiment with one black blade. Given the importance of the appearance of the landscape to those viewing it, the former option is preferable.
By Staffan Engström, Managing Director, Ägir Konsult, Sweden
- Category: Articles
A Road Map to Successful and Conclusive Wind Turbine Improvement Projects
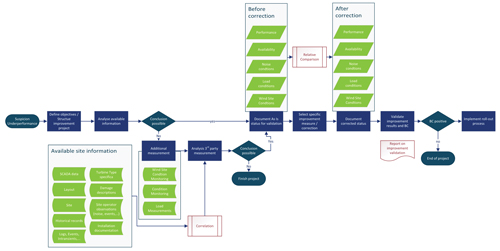
By Karl Fatrdla, Power Factors and Karl Fatrdla Consulting, Austria
- Category: Articles
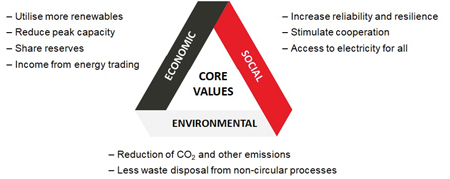
Electricity is frequently called the lifeblood of modern society, providing us with everyday comfort, security and mobility. Electricity networks are the ‘blood vessels’ which deliver the electricity to our homes, factories and trains. They have been built for over a century and evolved into the largest and most complex machine ever made by humanity.
By Alexandre Oudalov, Market Innovation, Hitachi ABB Power Grids
Use of cookies
Windtech International wants to make your visit to our website as pleasant as possible. That is why we place cookies on your computer that remember your preferences. With anonymous information about your site use you also help us to improve the website. Of course we will ask for your permission first. Click Accept to use all functions of the Windtech International website.