- Category: Articles
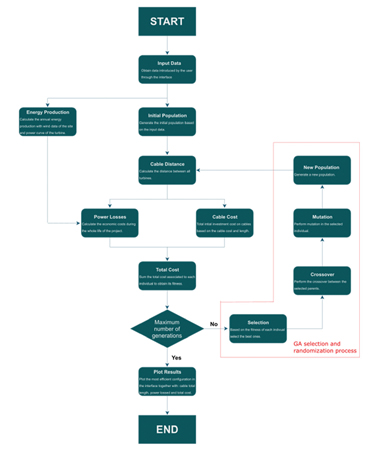
The offshore wind industry has developed rapidly during recent years and is expected to continue expanding over the coming decades. The industry is moving forward, and bigger wind farms are being installed all over the world. Despite the increase in the number of wind farms, the initial investments and operation costs are still relatively high. Reducing the total costs associated with offshore wind farms is crucial to limit economic risks and attract new investors. One of the most notable parts of the total cost is associated with electricity exportation, which is highly influenced by the strategy defined to interconnect the turbines. With the objective of reducing these costs, this article presents a genetic-algorithm-based techno-economic tool that optimises the electric layout considering the loss of revenue due to electric losses inside the wind farm and the purchasing cost of electric cables.
By Mikel Rosell Diez, Engineer, IDOM Consulting, Engineering, Architecture, Spain
- Category: Articles
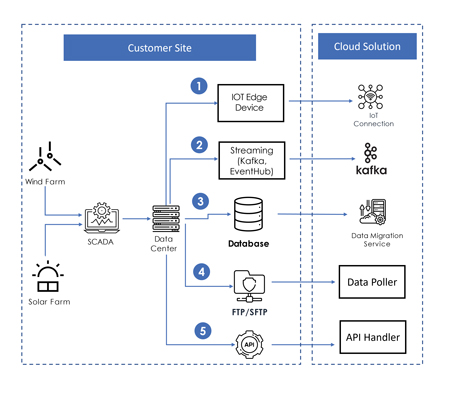
As the cumulative deployment of renewable energy grows, digital solutions for renewable asset management and analytics are becoming increasingly popular. Data accessibility and data quality serve as system cornerstones.
By Feng Zhang and Gopi Maniachari, Utopus Insights, USA
- Category: Articles
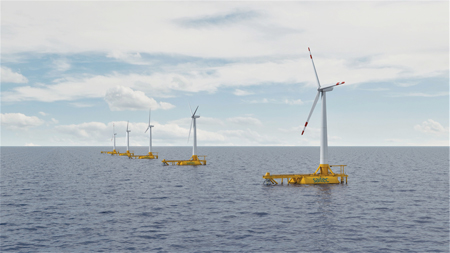
A structural health monitoring system has been developed to detect damage in the mooring system of floating wind turbines by analysing the movement of the platform. A cost-effective smart sensor that combines a global navigation satellite system and an inertial navigation unit is used. The collected data is used to create mathematical models when the system is healthy. After the so-called learning period, new incoming data feeds the models, which in turn evaluate the behaviour of the platform compared with the reference situation. If the difference exceeds a threshold, damage in the mooring system is assumed.
By Jon Basurko, Researcher, IKERLAN BRTA, Spain
- Category: Articles
The Aerosense Data Gateway – An Open-Source Turbine-To-Cloud Data Engineering Example
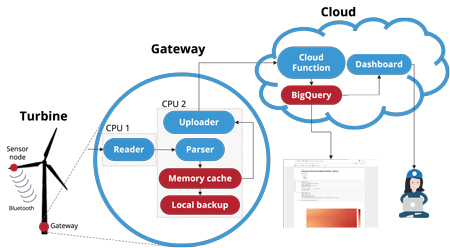
By Marcus Lugg, Senior Software Engineer, Octue, UK
- Category: Articles
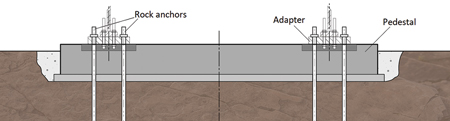
CTE Wind acted as an independent reviewer of an onshore rock adapter wind turbine foundation design for a wind farm in a Scandinavian country. During the analysis it was observed that including the tower stiffness in the numerical models was critical to accurately capture the structure’s behaviour. The tower stiffness was taken into account by modelling a segment of its actual geometry. The simulations showed that the rock anchors in the original design did not meet the safety requirements in terms of tensile strength. The reasons for the divergence in results are explored in this article.
By David Alegre Gimeno, Senior Engineer, CTE Wind Civil Engineering, France
- Category: Articles
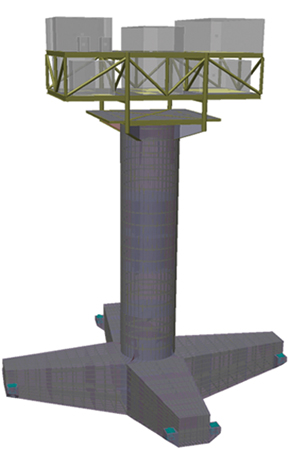
Floating wind farms will be an important contributor to the growth of renewable energy production, giving access to new areas in deep water with high mean wind speeds. To date, floating offshore wind farms have progressed from individual test turbines to small groups of individual turbines near to shore. The next significant advance in floating wind will be pilot projects, expected to be of around 250MW. These will be in deeper water located further from land and will therefore require a substation to step up the voltage for transmission to shore. The challenges of designing a structurally efficient low-motion vessel are greater for the small topside weight and footprint of the electrical equipment for 250MW than they are for a commercial-scale floating substation of 1GW. Different options for the floater design are discussed and compared. A minimum structure tension leg platform was found to provide low motion combined with minimum structural weight.
By Justin Jones, Civil and Structural Group Manager, Petrofac, UK
- Category: Articles
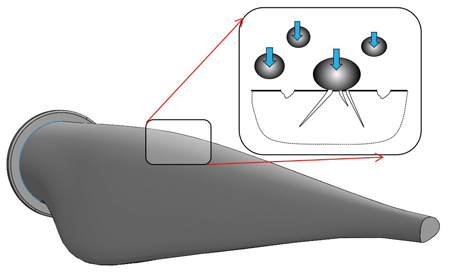
Wind turbines are subject to high mechanical and environmental loads, including extreme winds, storms, rain, gravitational load on rotating blades, and temperature and humidity variations. These loads lead to the degradation of wind turbine parts, in particular wind turbine blades. Repair of wind turbine blades can cost many thousands of dollars. Such high costs can influence the wind energy costs in general. Thus, efficient repair of wind turbines is an important element of the renewable energy transition, making wind energy more competitive. In this article, mechanisms of wind turbine blade degradation, repair technologies and possibilities to reduce the repair costs are reviewed.
By Leon Mishnaevsky Jr, Senior Scientist, Technical University of Denmark, Denmark
Use of cookies
Windtech International wants to make your visit to our website as pleasant as possible. That is why we place cookies on your computer that remember your preferences. With anonymous information about your site use you also help us to improve the website. Of course we will ask for your permission first. Click Accept to use all functions of the Windtech International website.