A Review of the Status and Risks of Floating Wind Turbine Technology
The floating wind turbine platforms (FWTP) industry is at an early and exciting stage. There are a number of emerging designs and a mix of platform and wind turbine types. It is also encouraging to see high levels of collaboration, with many companies working alongside bodies such as the Energy Technologies Institute, National Renewable Energy Laboratory, NOWITECH, Risø and the University of Maine. This article is a summary of a major report conducted by the author, which provides an up-to-date review of the FWTP industry and its principle technical risks.
By Charles Briggs, Renewable Energy Consultant, SgurrEnergy, UK
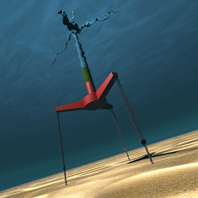
By Charles Briggs, Renewable Energy Consultant, SgurrEnergy, UK