Thinking Outside the Box
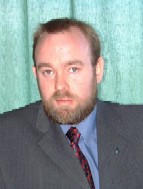
By Steven Peace, Eurowind Small Turbines Ltd, UK
There are numerous small wind turbines available on the market ranging from a few hundred watts to a few hundred kilowatts, almost all of which are horizontal axis wind turbines (HAWTs). The smallest of these machines are really only meant to be used for charging batteries on caravans or boats, although some have been appearing on remote street lights, signs and telephone boxes that have a minimal power requirement. The 1 to 15kW range are designed mainly for use on remote, off-grid, individual properties or smallholdings, whereas those of 15kW upwards are aimed at small remote communities. None of the conventional HAWTs are really designed for use within the built environment.
HAWTs are not well suited to the turbulent wind found in built-up areas and can be observed constantly hunting for the wind direction and rarely settling in one position for very long. This leads to inefficient power generation and excessive fluctuation in their power supply.
Over the last year or so, there have been a number of real alternatives appearing on the market, generally in the under 3kW range, most based upon one or another of the vertical axis wind turbine (VAWT) principles.
Current large HAWTs are well developed, highly sophisticated machines. All the big manufacturers are trying desperately to further refine them and squeeze every little bit of extra power and efficiency out of them. However, the truth is that, apart from the odd tweak here and there, the HAWTs are rapidly reaching the limits of their viability.
The blades are a particular problem. Modern turbine blades are largely handmade and can take anything up to 8 to 10 days each to produce. The logistics of moving and erecting a 61.5m blade in one piece are horrendous, and virtually impossible by road; therefore, the factories that produce these larger blades need to be located by the sea. Furthermore, as a wind turbine’s output is directly related to the swept area of its blades, if HAWTs are to grow any bigger even larger blades will be required. Using conventional materials (i.e. glass fibre) the blades have more or less reached their limits; larger blades can be built for HAWTs, but they will require more exotic materials such as carbon fibre, which, because of the nature of the materials and supply problems, will probably make the cost of these blades unviable.
Added to the blade problems, the large machines require a relatively high degree of maintenance and there are issues with gearboxes, bearings and support towers, all of which are struggling to keep pace with the ever larger sizes, weights and stresses of these latest HAWTs.
Currently, outside pressures on the industry by governments committed to high targets of renewable energy production agreed at Kyoto are pushing the industry forward. Understandably though, the wind farm developers would also like to have larger machines to maximise profits and take advantage of the economies of scale. The technology of HAWTs is rapidly reaching a plateau and soon the manufacturers will not be able to keep up with demand. However, why should they worry when they can easily sell every machine they can build? It is the governments and wind farm developers who will inevitably suffer, not being able to meet their targets and having to pay more as the market forces of supply and demand gradually creep the prices up.
There is an obvious solution: if the industry were to switch just a fraction of its research and development resources and funding to work on the relatively unexplored technology of VAWTs (when compared to HAWTs), then machines with outputs of 10 to 20MW or more could be in production in less than 5 years.
Unless there is a shift in policy and the big players are prepared to think outside the box by embracing such innovations, the current industry might find it is ‘scoring an own goal’ and being left behind.